REX-CUT HAS YOU COVERED:
Robotic blending of laser brazed seams in automotive roof joints is a specialty application that utilizes varying abrasive wheel thicknesses to get the job done right. Major abrasive wheel manufacturers offer standard thickness, but this custom automotive finishing process calls for wheel specifications that are tough to come by.
What typically happens is that distributors step in and surface grind abrasive wheels down to the size required; but this adds tremendous labor costs to the value chain, which are almost always passed on to customers.
Rex-Cut recognized that this is not the most efficient way to get automotive manufactures the wheels they need. That’s why we offer a variety of custom thickness wheels specifically designed to match the growing needs of the automotive industry.
Need a specific wheel thickness? Just ask us. We can manufacture large volume custom type 1 wheel orders with a turnaround time of just 2-4 weeks.
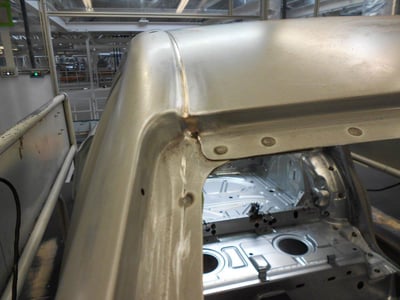
QUALITY WHEELS FOR A DEMANDING INDUSTRY:
To keep production lines running smoothly, tolerances on abrasive wheels must be right the first time. Any deviations in wheel thicknesses will be detected by the automation software on an automotive assembly line and delay operations. Rex-Cut follows strict quality control procedures at every step of wheel production, from fabric to finishing processes. The result is that our wheels hold a tolerance of ten thousandths of an inch. This is unmatched by any other blending wheel and guarantees smooth workflow at any production facility.
Our wheels are also manufactured using a unique process that creates a higher quality wheel. Typical grinding wheels are made from non-woven nylon, which consists of an open nylon filament web that has an abrasive grain mounted to it using a bonding agent. The problem is that non-woven nylon wears out relatively quickly and requires frequent replacement.
Rex-Cut uses a non-woven cotton fiber that’s denser than non-woven nylon, lasts longer, and enables greater efficiency. Non-woven cotton fiber wheels cost about the same as non-woven nylon, but they last 2-3 times longer. Workflow efficiency benefits because this longer lifespan minimizes wheel changes, and that means less downtime.
Other added benefits to using cotton fiber wheels are the quality and consistency of the finish they provide, and the quickness of braze removal. A single wheel can take down welds quickly and leave smooth, paintable finishes on a long line of cars. For automotive braze removal applications, switching to a cotton wheel is a change that has a big impact on smooth line operations, while also shrinking abrasive costs and time spent changing wheels.
Why grind down wheel after wheel, trying to fit a square peg into a round hole? Rex-Cut wheels will fit your seam joint when you order them, and we can deliver the thickness you need to perform precision braze removal in almost any automotive application.
QUESTIONS?:
Talk to our application experts today. We can work with you to see if our abrasives can help your application in any way.